1. Introduzione
Nel panorama industriale contemporaneo, la meccanica di precisione gioca un ruolo di primo piano, rappresentando uno dei pilastri fondamentali per la crescita tecnologica e la competitività delle imprese. Con l’avvento di processi sempre più automatizzati e la necessità di realizzare componenti dalle tolleranze minime, la meccanica di precisione diventa un requisito imprescindibile in numerosi settori, dall’aerospaziale al medicale, dall’automotive fino a toccare la robotica e le linee di produzione su larga scala.
Parlare di meccanica di precisione non significa soltanto riferirsi a lavorazioni meccaniche avanzate, macchinari all’avanguardia o l’uso di materiali innovativi; significa anche enfatizzare l’importanza di un’approfondita competenza tecnica e di un rigoroso controllo qualità in ogni fase del processo produttivo. Le aziende che operano in quest’ambito sanno bene quanto siano cruciali l’esperienza, l’innovazione e la capacità di rispondere in modo flessibile alle esigenze dei clienti.
In Italia, la tradizione manifatturiera ha sempre ricoperto un ruolo di eccellenza a livello internazionale. Regioni come la Puglia, ad esempio, vantano un tessuto industriale e artigianale ricco di competenze, esperienza e know-how specializzato, che si esprimono al meglio proprio nei processi di meccanica di precisione. Puglia Meccanica, con sede nel cuore di questa regione, incarna appieno questi valori, offrendo un’ampia gamma di servizi che spaziano dalla tornitura e fresatura a controllo numerico, fino all’assemblaggio di parti complesse e ai trattamenti superficiali.
Ma quali sono gli aspetti che rendono la meccanica di precisione un tassello così indispensabile per l’industria moderna?
Per rispondere a questa domanda, occorre considerare molteplici fattori: dai vantaggi competitivi legati alla riduzione dei difetti di produzione, all’ottimizzazione dell’impiego di risorse e materiali, fino all’importanza di integrare innovazioni come la digitalizzazione e l’automazione dei processi produttivi (Industria 4.0). Allo stesso tempo, bisogna riconoscere l’importanza di un approccio orientato alla sostenibilità e alla responsabilità sociale, che include l’utilizzo consapevole di energia e materie prime, nonché una visione di lungo termine per ridurre l’impatto ambientale.
In un mondo in cui l’innovazione corre veloce e la concorrenza diventa sempre più agguerrita, investire nella meccanica di precisione significa porre le basi per un futuro solido, in cui la qualità e l’affidabilità dei prodotti rappresentano il vero valore aggiunto. Scopriamo insieme perché.
2. Cos’è la meccanica di precisione e perché è fondamentale nell’industria moderna
2.1 Definizione di meccanica di precisione
La meccanica di precisione è un ramo della meccanica che si occupa della progettazione, produzione e manutenzione di componenti e sistemi caratterizzati da tolleranze estremamente ridotte e finiture superficiali di elevata qualità. L’obiettivo principale è minimizzare gli errori dimensionali e geometrici in modo che i pezzi finiti rispondano a specifiche rigorose, spesso nell’ordine dei millesimi di millimetro o anche meno. Quando si parla di “precisione”, si fa riferimento non solo alla geometria del pezzo (diametri, spessori, allineamenti, ecc.), ma anche alla qualità delle superfici, ai trattamenti termici e ai parametri metallurgici che possono influenzare le prestazioni del prodotto.
La meccanica di precisione può essere vista come l’evoluzione e la specializzazione della meccanica tradizionale, arricchita da strumenti di misura sofisticati e macchinari a controllo numerico (CNC), in grado di eseguire movimenti e lavorazioni complesse con margini di errore decisamente contenuti. Questa disciplina non si limita alle sole operazioni di tornitura e fresatura, ma include anche processi come la rettifica, l’elettroerosione (EDM), la levigatura e i trattamenti termici e superficiali specifici. Ognuno di questi step è pensato per garantire che il pezzo finale risponda esattamente alle specifiche desiderate.
2.2 Breve cenno storico (h3)
Le origini della meccanica di precisione si possono far risalire alla rivoluzione industriale del XVIII secolo, quando nacquero le prime macchine utensili in grado di standardizzare la produzione di componenti meccanici. Con l’introduzione di torni e fresatrici sempre più sofisticati, si iniziarono a produrre pezzi che, in precedenza, richiedevano lunghi tempi di fabbricazione e un elevato intervento manuale. Questa spinta verso la standardizzazione e l’automazione segnò l’inizio di un processo evolutivo che, nel corso dei decenni, portò all’introduzione dei controlli numerici e, successivamente, dei CNC.
Nel XX secolo, con il boom dell’industria automobilistica e aerospaziale, la domanda di componenti ad altissima precisione crebbe esponenzialmente. L’avvento di macchine a controllo numerico, sensori di misura digitali e software di progettazione CAD/CAM ha poi portato a un ulteriore salto di qualità. Oggi, la meccanica di precisione non è più un settore di nicchia, bensì un elemento chiave nella competitività e nell’innovazione dell’industria manifatturiera mondiale.
2.3 Importanza nell’industria moderna (h3)
Nell’era dell’Industria 4.0, la precisione non è semplicemente un requisito “auspicabile”, ma una necessità fondamentale. La digitalizzazione dei processi produttivi, l’analisi dei dati in tempo reale e l’interconnessione tra macchine e sistemi di gestione richiedono componenti e impianti che possano funzionare in maniera affidabile e continuativa. Difetti di fabbricazione, scostamenti dalle specifiche o tolleranze eccessive possono tradursi in guasti, ritardi nella produzione o addirittura richiamo di prodotti, con conseguente danno economico e reputazionale.
Un altro aspetto cruciale è la ricerca continua dell’efficienza: componenti di precisione consentono di ridurre gli scarti di lavorazione, migliorare l’accoppiamento tra parti meccaniche e, in generale, innalzare la produttività delle linee di montaggio. In tal senso, la meccanica di precisione rappresenta un investimento strategico, poiché permette di mantenere elevati standard qualitativi e, allo stesso tempo, contenere costi legati a manutenzioni straordinarie e difettosità.
3. Applicazioni pratiche: il ruolo della meccanica di precisione in diversi settori
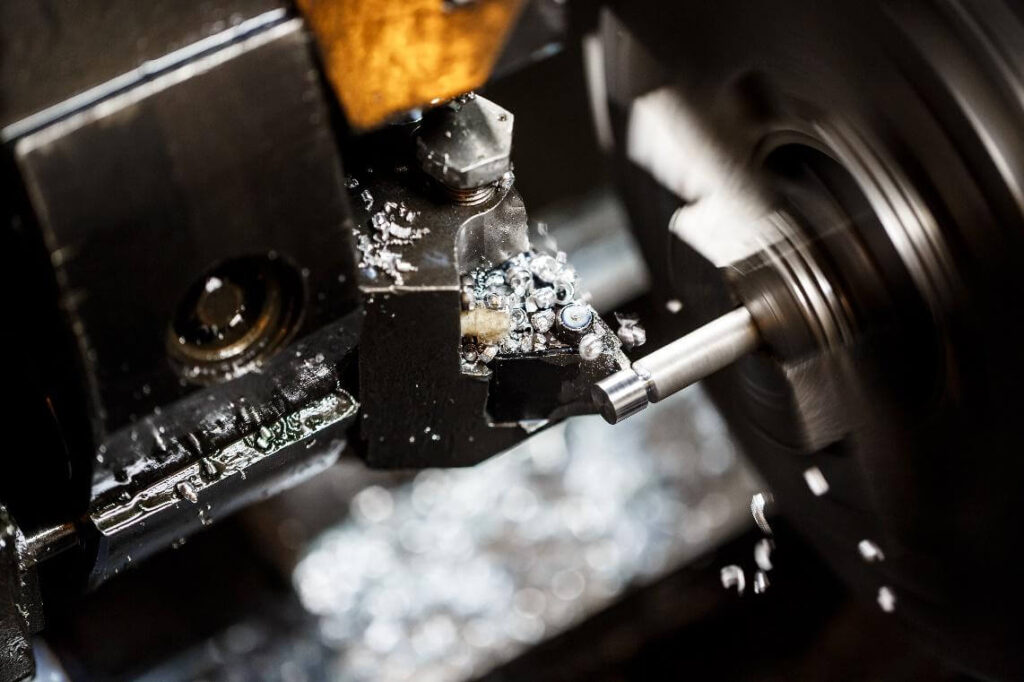
3.1 Settore aerospaziale
Il settore aerospaziale è probabilmente uno dei contesti in cui la meccanica di precisione assume la massima importanza. Aerei, elicotteri, navicelle spaziali e droni richiedono componenti in grado di sostenere stress e temperature estreme, garantendo al contempo un peso ridotto per ottimizzare i consumi e la manovrabilità. Pensiamo, ad esempio, alle turbine dei motori aeronautici, alle pale delle eliche o ai dispositivi di controllo del volo: tutte queste parti devono essere prodotte con livelli di accuratezza straordinari, al fine di ridurre al minimo vibrazioni, attriti e fenomeni di usura.
La sicurezza è un altro fattore determinante: un semplice errore millimetrico nella costruzione di un componente critico può tradursi in un guasto potenzialmente letale. Per questo motivo, l’industria aerospaziale applica rigidi standard di certificazione, come ad esempio la normativa AS9100, che richiedono un controllo qualità estremamente severo lungo l’intera filiera produttiva. Un’azienda specializzata in meccanica di precisione, come Puglia Meccanica, può apportare competenze e attrezzature adeguate per soddisfare tali requisiti, fornendo componenti realizzati con materiali avanzati (leghe di titanio, alluminio aerospaziale, compositi) e sottoposti a trattamenti termici e superficiali di alto livello.
3.2 Automotive
Nel settore automotive, la concorrenza e la pressione sui costi sono altissime. Al tempo stesso, i consumatori e le normative governative richiedono veicoli più sicuri, efficienti e sostenibili. I motori a combustione interna di ultima generazione, i sistemi ibridi e i motori elettrici, così come i sistemi di trasmissione e sospensione, includono numerosi componenti che necessitano di lavorazioni di precisione: alberi, ingranaggi, pistoni, cilindri, cuscinetti, solo per citarne alcuni.
Le case automobilistiche investono in ricerca e sviluppo per ridurre pesi, attriti e consumi, migliorando al contempo le prestazioni e il comfort di guida. Per raggiungere questi obiettivi, i fornitori di componenti devono rispettare tolleranze molto strette e assicurare un’elevata qualità di finitura, riducendo vibrazioni e rumori. L’automazione delle linee di montaggio, inoltre, richiede parti standardizzate che possano essere assemblate in tempi ridotti, senza richiedere aggiustamenti manuali. In questo contesto, la meccanica di precisione costituisce un vantaggio competitivo inestimabile, sia per i produttori finali sia per i fornitori di primo e secondo livello.
3.3 Medicale e biomedicale
Il settore medicale e biomedicale è un altro ambito in cui la precisione è vitale. Strumenti chirurgici, protesi, impianti ortopedici, dispositivi per la diagnosi: tutti questi elementi devono rispondere a standard di sicurezza e affidabilità estremamente elevati. Pensiamo, ad esempio, a un impianto protesico per un’articolazione del ginocchio o dell’anca: se le tolleranze non fossero rispettate, il paziente potrebbe subire dolore, infiammazioni o dover affrontare interventi correttivi. Analogamente, le apparecchiature di diagnostica per immagini, come TAC e risonanze magnetiche, necessitano di componenti in metalli speciali o polimeri high-tech, lavorati con una cura maniacale al dettaglio.
Oltre alla precisione dimensionale, in campo biomedicale assume grande rilievo la scelta dei materiali biocompatibili e la qualità delle superfici. Spesso vengono utilizzate leghe di titanio o acciai inossidabili chirurgici, trattati in modo da prevenire la corrosione e garantire la massima igiene. La meccanica di precisione, in questo caso, si sposa con la necessità di un rigoroso controllo delle contaminazioni, imponendo ambienti di produzione sterili o quantomeno altamente puliti, in cui l’errore e la contaminazione devono essere ridotti praticamente a zero.
3.4 Industria manifatturiera e robotica
Il termine “industria manifatturiera” è molto ampio e può includere svariati comparti, dall’alimentare al tessile, dall’elettronica alla produzione di beni di largo consumo. C’è però un aspetto comune che accomuna molti di questi settori: l’automazione dei processi. Le linee di montaggio automatizzate, i bracci robotici e le macchine CNC richiedono componenti meccanici ad alta precisione per operare correttamente e raggiungere gli obiettivi di produttività prefissati.
Un robot industriale, ad esempio, è dotato di numerosi snodi e giunti, ciascuno con motori e sensori che devono funzionare in perfetta sincronia. Eventuali giochi o imprecisioni nei movimenti si traducono in errori di posizionamento, riducendo la qualità del prodotto finito o rallentando l’intero ciclo di produzione. Ecco perché la meccanica di precisione risulta determinante: componenti lavorati al millesimo e controllati in ogni dettaglio sono in grado di garantire movimenti fluidi e ripetibili, riducendo al minimo gli interventi di manutenzione.
Allo stesso modo, le macchine automatiche per l’imballaggio o il confezionamento alimentare si basano su nastri trasportatori, sistemi di dosaggio e di taglio, che richiedono anch’essi precisione per evitare sprechi di prodotto o difetti di confezionamento. L’approccio “lean” alla produzione, poi, enfatizza ulteriormente la necessità di eliminare gli sprechi e ottimizzare l’utilizzo di risorse, obiettivi che solo processi ben ingegnerizzati e componenti affidabili possono rendere possibili.
4. Tecnologia e processi fondamentali nella meccanica di precisione
4.1 Metodi di lavorazione avanzati
Le principali tecnologie di lavorazione impiegate nella meccanica di precisione includono:
- Tornitura: Consiste nella rimozione di materiale da un pezzo in rotazione, spesso utilizzata per realizzare elementi cilindrici o conici (alberi, boccole, alberini per motori, ecc.). Oggi le torni CNC sono in grado di raggiungere tolleranze di pochi micron e di gestire geometrie complesse grazie a torrette con utensili multipli.
- Fresatura: Con la fresatura si asportano trucioli da un pezzo fermo (o in movimento controllato) per ottenere superfici piane, cave, spallamenti, forature e altre lavorazioni. I centri di lavoro CNC a più assi permettono di eseguire, in un’unica macchina, lavorazioni multiple e complesse, riducendo tempi e rischi di errore dovuti al riposizionamento manuale.
- Rettifica: Processo che impiega mole abrasive per ottenere superfici estremamente precise in termini di finitura e tolleranza dimensionale. È fondamentale per componenti che richiedono superfici di contatto ad elevata uniformità o accoppiamenti perfetti, come cuscinetti e ingranaggi ad alte prestazioni.
- Elettroerosione (EDM): Sfrutta l’erosione controllata del metallo mediante scariche elettriche tra un elettrodo e il pezzo da lavorare, immersi in un dielettrico. È una tecnologia particolarmente utile per lavorare materiali duri e leghe speciali, o per produrre geometrie molto complesse (come cavità e fori di precisione).
- Taglio laser e a getto d’acqua: Questi metodi consentono di sagomare pezzi con profili anche molto complessi. Sono ideali per prototipazione rapida, lamierati e particolari di piccole o medie dimensioni, laddove la precisione di taglio e la velocità di esecuzione risultano fondamentali.
- Additive Manufacturing: Anche se più recente, la stampa 3D (in metallo o plastica) si affaccia nel mondo della meccanica di precisione come soluzione innovativa, soprattutto in applicazioni particolari o per la realizzazione di prototipi. Tuttavia, la necessità di post-lavorazioni (rettifica, fresatura, tornitura) per raggiungere le tolleranze richieste rimane spesso imprescindibile.
4.2 Materiali e trattamenti superficiali
Selezionare il materiale giusto è una delle fasi fondamentali nella progettazione e realizzazione di un componente di precisione. In base all’applicazione, è possibile scegliere tra acciai speciali, leghe di alluminio, leghe di titanio, materie plastiche tecniche, polimeri rinforzati con fibre di carbonio o vetro, e così via. Ognuno di questi materiali presenta proprietà meccaniche, termiche e chimiche specifiche che ne determinano l’idoneità per una determinata funzione.
Una volta scelto il materiale, si può intervenire con trattamenti termici (tempra, rinvenimento, cementazione, nitrurazione) per aumentare la durezza superficiale o migliorare la resistenza a usura e fatica. Allo stesso modo, i trattamenti superficiali (galvanici, chimici, fisici) consentono di conferire al pezzo proprietà aggiuntive, come resistenza alla corrosione, riduzione degli attriti, miglioramento dell’estetica o compatibilità con ambienti particolarmente aggressivi. In ambito medicale, ad esempio, rivestimenti come la ceramica o il titanio anodizzato sono molto diffusi per motivi di biocompatibilità e igiene.
4.3 Sistemi di controllo qualità
Per verificare che i componenti prodotti rispettino le tolleranze specificate, è essenziale disporre di strumenti e procedure di controllo qualità adeguati. Le moderne aziende di meccanica di precisione si dotano di macchine di misura a coordinate (CMM), proiettori di profili, rugosimetri, calibri digitali ad alta accuratezza e altri apparecchi di metrologia avanzata. Il controllo qualità può avvenire sia in-process (cioè durante la lavorazione), sia a fine processo, per garantire la conformità del prodotto prima della consegna.
Oltre alla dotazione hardware, le certificazioni (ISO 9001, ISO 14001, ISO 45001 e, in contesti specifici, AS9100 o ISO 13485) attestano la capacità dell’azienda di operare secondo standard riconosciuti a livello internazionale. Queste certificazioni riguardano la qualità, l’ambiente e la sicurezza, e rappresentano un valore aggiunto significativo per i clienti che cercano partner affidabili e orientati al miglioramento continuo.
5. Trend e futuro della meccanica di precisione
5.1 Digitalizzazione e Industria 4.0
Uno dei trend più rilevanti nel campo della meccanica di precisione riguarda la digitalizzazione dei processi produttivi, in linea con i principi dell’Industria 4.0. Le macchine CNC di ultima generazione sono sempre più interconnesse e dialogano con software gestionali e sistemi di analisi in tempo reale. Questo permette di:
- Monitorare costantemente parametri come temperature, vibrazioni, consumi energetici, usura degli utensili, riducendo i fermi macchina e i difetti di lavorazione.
- Ottimizzare i cicli di lavoro, identificando in anticipo eventuali colli di bottiglia e migliorando la pianificazione della produzione.
- Integrare i dati produttivi con sistemi di gestione aziendale (ERP, MES), consentendo di avere una visione a 360° su costi, tempi e qualità.
Questi aspetti, uniti all’utilizzo di algoritmi di intelligenza artificiale e machine learning, aprono la strada a una meccanica di precisione sempre più smart, in cui la manutenzione predittiva, la riduzione degli scarti e la personalizzazione del prodotto diventano elementi distintivi.
6.2 Ricerca e sviluppo di nuovi materiali
Un’altra direttrice di sviluppo riguarda i nuovi materiali. Le tradizionali leghe metalliche (acciai, alluminio, titanio) vengono costantemente migliorate e affiancate da materiali compositi avanzati (fibre di carbonio, fibre di vetro, polimeri rinforzati) che offrono prestazioni superiori in termini di leggerezza, resistenza e durabilità. La sfida, in questo caso, consiste nell’adattare i processi di lavorazione a materiali che presentano proprietà fisico-meccaniche del tutto differenti da quelle dei metalli. La stampa 3D in metallo e polimeri high-tech si sta poi affermando come tecnologia complementare, specialmente in fase di prototipazione o per geometrie molto complesse, anche se la post-lavorazione resta spesso fondamentale per raggiungere la precisione richiesta.
6.3 Sostenibilità e responsabilità sociale
La sostenibilità ambientale e la responsabilità sociale d’impresa (RSI) sono temi sempre più centrali nel dibattito industriale. La meccanica di precisione può fornire un contributo significativo in tal senso, consentendo di ridurre gli sprechi di materiale, l’uso di energia e il numero di scarti prodotti. Macchinari moderni e processi ottimizzati migliorano l’efficienza energetica, mentre l’impiego di materiali più leggeri o riciclabili influisce positivamente sul ciclo di vita del prodotto.
Per molte aziende, inoltre, l’adozione di politiche di RSI costituisce un fattore competitivo, specialmente nei mercati internazionali più evoluti, dove i clienti prestano grande attenzione all’impatto ambientale e sociale dei fornitori. Le certificazioni ambientali (ISO 14001) e i codici di condotta etici dimostrano un impegno concreto verso una produzione responsabile, che integra gli obiettivi di crescita con il rispetto per l’ambiente e la società.