La meccanica di precisione è sempre stata un settore strategico per lo sviluppo industriale, caratterizzato da standard di qualità molto elevati e da una continua ricerca di innovazione per ottimizzare processi e prodotti.
Negli ultimi anni, la digitalizzazione ha rivoluzionato profondamente questo comparto, portando con sé nuove tecnologie, strumenti e metodologie che hanno contribuito a trasformare radicalmente la progettazione, la produzione e la gestione dei sistemi meccanici.
In questo articolo, analizzeremo l’impatto della digitalizzazione sulla meccanica di precisione, approfondendo le principali applicazioni, i benefici, le sfide e le opportunità future.
L’avvento della digitalizzazione nella meccanica di precisione
L’innovazione digitale in ambito industriale non è un fenomeno recente, ma è negli ultimi due decenni che ha subito un’accelerazione esponenziale. L’evoluzione dell’elettronica, dell’informatica e delle telecomunicazioni ha aperto la strada a nuove tecnologie che hanno permesso alle aziende meccaniche di precisione di cambiare il proprio paradigma produttivo.
Tra le tecnologie più rilevanti troviamo:
- Sistemi CAD/CAM: permettono di progettare componenti e attrezzature in ambiente virtuale, con simulazioni precise e test preliminari che riducono costi e tempi.
- Macchine CNC di ultima generazione: consentono lavorazioni estremamente accurate e veloci, grazie a controlli numerici di precisione e software specializzati.
- Robotica avanzata e cobot: i robot collaborativi, dotati di intelligenza artificiale, lavorano a fianco degli operatori umani per migliorare efficienza e sicurezza.
- Internet of Things (IoT): i sensori e i dispositivi connessi raccolgono dati in tempo reale, permettendo di monitorare processi, consumi e performance dei macchinari.
- Big Data e Analytics: l’analisi di grandi quantità di dati consente di prevedere guasti, ottimizzare la produzione e personalizzare i processi in base a esigenze specifiche.
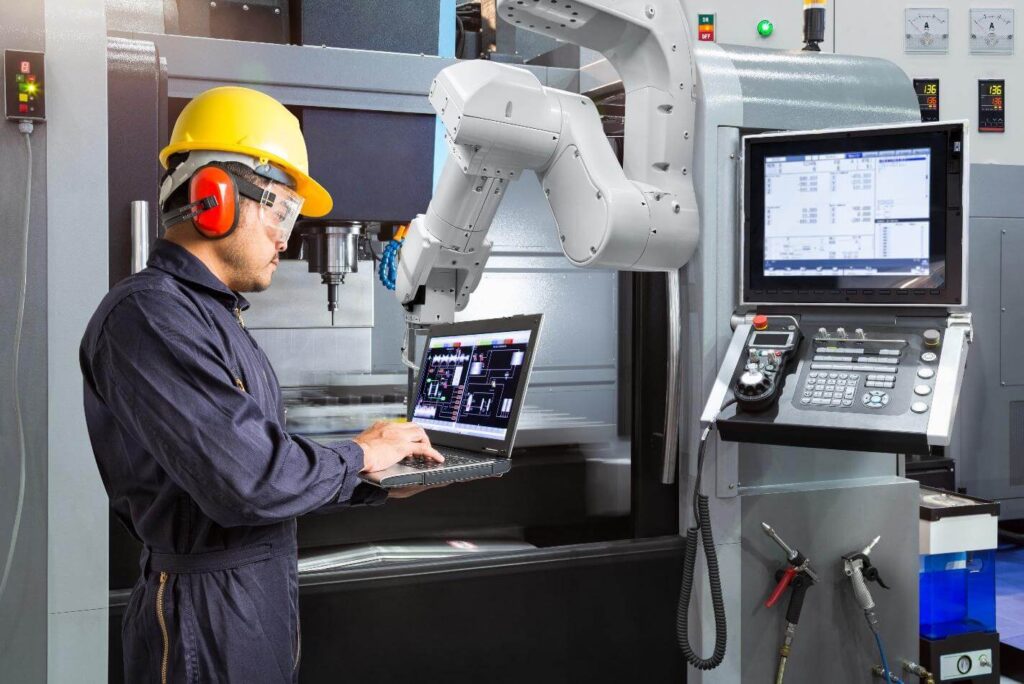
Benefici tangibili della digitalizzazione nella produzione
L’introduzione di strumenti digitali nella meccanica di precisione ha portato a una serie di benefici concreti per le aziende, con ricadute positive su più livelli.
Maggiore efficienza e velocità di lavorazione
L’automazione e la robotica consentono di ridurre i tempi di setup delle macchine e di eseguire lavorazioni complesse in tempi molto più rapidi. Le macchine CNC, integrate con i software CAD/CAM, permettono di passare dalla fase progettuale alla produzione in poche ore, con una precisione centesimale o addirittura micronica. Questa velocizzazione dei processi si traduce in un aumento della capacità produttiva e in una maggiore competitività sul mercato.
Riduzione dei costi operativi
La digitalizzazione consente di ottimizzare l’uso delle risorse e di monitorare in tempo reale lo stato delle lavorazioni. Grazie all’IoT, è possibile individuare tempestivamente eventuali inefficienze o malfunzionamenti, riducendo sprechi di materiale e di energia. Inoltre, l’analisi dei dati raccolti permette di pianificare la manutenzione in modo predittivo, evitando costosi fermi impianto dovuti a guasti improvvisi.
Qualità e controllo migliorati
La meccanica di precisione si contraddistingue per la necessità di garantire standard qualitativi elevatissimi. Con l’introduzione di sistemi di visione artificiale, sensori e software di analisi in tempo reale, è possibile effettuare controlli metrologici e rilevazioni durante ogni fase del processo produttivo. In questo modo, gli scostamenti dalla tolleranza prevista vengono identificati immediatamente, consentendo di correggere gli errori e ridurre gli scarti.
Personalizzazione e flessibilità
Le aziende di meccanica di precisione possono oggi offrire soluzioni su misura per i propri clienti, grazie alla capacità di riconfigurare in modo rapido macchinari e linee produttive. Se prima era necessario mantenere stock elevati per far fronte alle diverse richieste, ora la produzione può essere gestita just-in-time, evitando l’accumulo di materiali e semilavorati in magazzino.
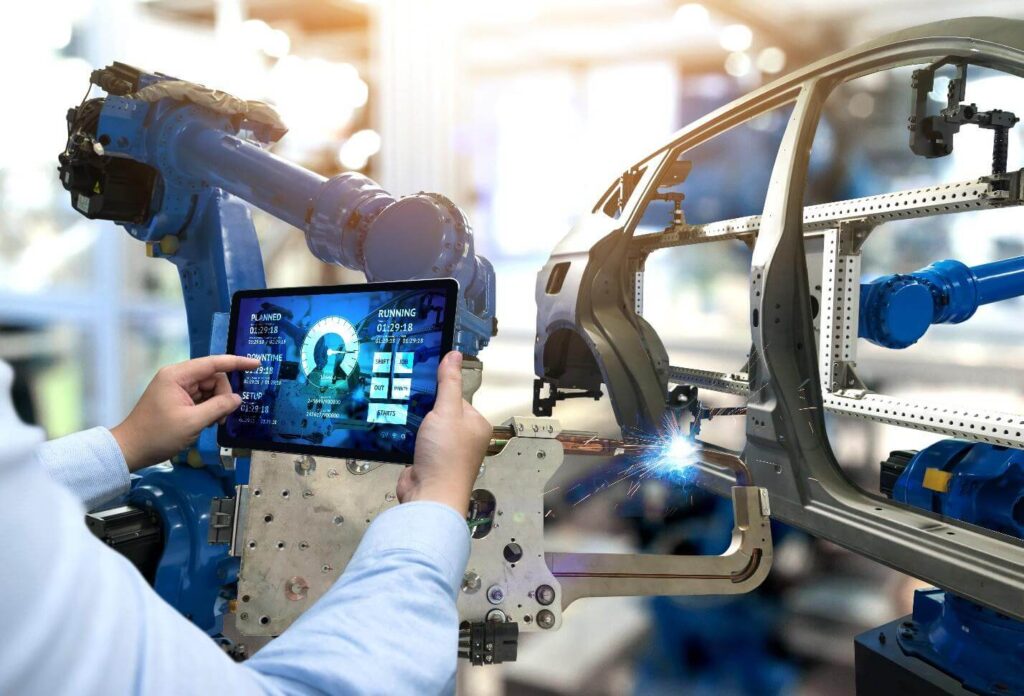
Tecnologie emergenti e nuove frontiere
Oltre alle tecnologie che già oggi trovano ampia applicazione, esistono alcune soluzioni emergenti che promettono di rivoluzionare ulteriormente il settore.
Digital twin e simulazioni avanzate
La creazione di gemelli digitali (digital twin) consente di replicare virtualmente un impianto o un componente, simulandone il comportamento nelle diverse condizioni operative. Questo approccio permette di testare nuovi processi, materiali o configurazioni senza rischi e senza costi eccessivi, accelerando l’innovazione e riducendo il time-to-market.
Additive manufacturing per la meccanica di precisione
La stampa 3D è già utilizzata in vari settori, ma sta diventando sempre più sofisticata per applicazioni che richiedono altissima precisione. Le nuove tecnologie di produzione additiva permettono di creare geometrie complesse e componenti leggeri, con proprietà meccaniche avanzate e tolleranze molto strette. Ciò apre prospettive interessanti per l’aerospaziale, l’automotive e il biomedicale.
Intelligenza Artificiale e machine learning
Le soluzioni basate sull’intelligenza artificiale offrono la possibilità di analizzare in modo automatico e predittivo grandi quantità di dati. Questo si traduce in un miglioramento continuo dei processi: i modelli di apprendimento consentono ai macchinari di autoregolarsi, identificando pattern di difetto o possibili inefficienze prima che si verifichino. L’AI può anche agevolare la pianificazione della produzione, ottimizzando l’uso di risorse e materiali.
Sfide e criticità della trasformazione digitale
Nonostante i numerosi vantaggi, la transizione verso una meccanica di precisione sempre più digitalizzata comporta anche alcune sfide che le aziende devono affrontare.
Investimenti iniziali e ammortamenti
L’adozione di macchinari all’avanguardia, sensori e software specializzati richiede investimenti significativi. Le piccole e medie imprese possono incontrare difficoltà nel reperire le risorse finanziarie necessarie e devono pianificare con attenzione l’adozione di nuove tecnologie, per evitare di rimanere indietro rispetto alla concorrenza.
Formazione del personale
La digitalizzazione introduce nuovi ruoli professionali e richiede competenze sempre più interdisciplinari. Gli operatori di macchina devono essere in grado di interfacciarsi con software di programmazione, sistemi di controllo e strumenti di analisi dati. Di conseguenza, le aziende devono investire nella formazione continua del proprio personale, promuovendo la crescita di competenze digitali e di problem-solving avanzato.
Cybersecurity e protezione dei dati
Con l’aumento dei dispositivi connessi, cresce anche il rischio di attacchi informatici e di furto di proprietà intellettuale. Le aziende specializzate in meccanica di precisione, che spesso operano in settori sensibili come l’aerospaziale o la difesa, devono adottare misure di sicurezza adeguate per proteggere i dati di progetto e le reti di produzione. L’implementazione di protocolli di sicurezza, crittografia e sistemi di monitoraggio costante risulta fondamentale per prevenire intrusioni e violazioni.
Evoluzione delle competenze e opportunità lavorative
La transizione digitale nel settore della meccanica di precisione sta creando nuove figure professionali, oltre a trasformare i ruoli tradizionali. Professionisti come i progettisti meccanici devono ora possedere conoscenze approfondite in ambito informatico e saper utilizzare software avanzati di simulazione, mentre i tecnici di produzione devono padroneggiare linguaggi di programmazione per macchine CNC e robot.
Parallelamente, si stanno diffondendo ruoli inediti, come gli esperti di analisi dati industriali (data analyst) o i responsabili dell’integrazione dei sistemi IoT, incaricati di gestire la grande mole di informazioni generata dai sensori. Queste nuove professionalità offrono opportunità di carriera interessanti per i giovani, consentendo di coniugare competenze ingegneristiche con quelle digitali.
Il ruolo della sostenibilità nella digitalizzazione
Un ulteriore aspetto da considerare è l’impatto ambientale. La meccanica di precisione, storicamente orientata a minimizzare gli scarti e a ottimizzare l’uso delle risorse, trova nella digitalizzazione un alleato prezioso per aumentare la sostenibilità dei processi. Grazie all’analisi dati, infatti, è possibile:
- Monitorare i consumi energetici e ridurli intervenendo sulle inefficienze.
- Sfruttare tecniche di manutenzione predittiva per allungare la vita utile dei macchinari.
- Migliorare la gestione della supply chain, limitando sprechi di materiale e trasporti inutili.
Questo approccio green non solo aiuta le aziende a ridurre i costi, ma risponde anche alle richieste di un mercato sempre più attento alle tematiche ambientali e sociali, contribuendo alla costruzione di un vantaggio competitivo e di un’immagine aziendale positiva.
Verso il futuro: prospettive e trend da seguire
La digitalizzazione della meccanica di precisione è un processo in costante evoluzione, destinato a trasformare ulteriormente il panorama produttivo nei prossimi anni. Alcuni trend che vale la pena tenere d’occhio includono:
- Smart factory e integrazione totale: l’obiettivo finale è quello di creare fabbriche intelligenti, in cui tutti i macchinari, i sistemi e i processi siano interconnessi e gestiti da piattaforme digitali centralizzate.
- Tecnologie di sensorizzazione avanzata: l’introduzione di sensori sempre più miniaturizzati e precisi amplierà le possibilità di monitoraggio in tempo reale, consentendo un controllo ancora più accurato dei parametri produttivi.
- Edge computing: la necessità di elaborare dati localmente, direttamente nei macchinari o nei dispositivi, ridurrà la latenza e migliorerà la reattività dei sistemi, favorendo l’implementazione di applicazioni di intelligenza artificiale e di controllo distribuito.
- Collaboration e open innovation: la complessità della digitalizzazione richiede collaborazione tra aziende, università, centri di ricerca e startup, favorendo la condivisione di competenze e soluzioni innovative.
Conclusioni
L’impatto della digitalizzazione sulla meccanica di precisione è ampio e profondo, coinvolgendo la progettazione, la produzione, il controllo qualità e la gestione dell’intera catena di fornitura. Grazie all’introduzione di tecnologie avanzate come CAD/CAM, CNC di ultima generazione, IoT e intelligenza artificiale, le aziende hanno l’opportunità di migliorare l’efficienza, la flessibilità e la competitività, offrendo prodotti sempre più performanti e personalizzati.
Tuttavia, la trasformazione digitale non è priva di sfide: richiede investimenti iniziali, un cambio di mentalità e un costante aggiornamento del personale, oltre a una maggiore attenzione alla sicurezza informatica. Chi saprà cogliere queste sfide e investirà in formazione, infrastrutture e ricerca, potrà posizionarsi in prima linea in un mercato globale in costante evoluzione.