Gli accoppiatori oleodinamici, noti anche come accoppiatori idrodinamici o fluid coupling, svolgono un ruolo fondamentale nella trasmissione di potenza tra motore e carico in numerosi settori industriali. Grazie al principio di funzionamento basato su olio o fluidi specifici, essi permettono di trasferire in modo graduale la coppia motrice, riducendo così picchi di sollecitazione, vibrazioni e usura meccanica.
Negli ultimi anni, l’evoluzione tecnologica ha portato a diversi miglioramenti rilevanti, sia sul fronte dei materiali sia su quello del design e dell’integrazione con i sistemi di controllo digitali. Oggi è possibile trovare sul mercato accoppiatori oleodinamici più leggeri, più efficienti e con funzionalità di monitoraggio avanzate che consentono di ottimizzare le prestazioni e la manutenzione.
Nel presente articolo esploreremo le innovazioni più recenti e le prospettive future, offrendo una panoramica completa e approfondita delle nuove soluzioni che stanno trasformando il settore.
Cosa sono gli accoppiatori oleodinamici e come funzionano?
Prima di addentrarci nelle ultime novità, è utile ripassare il principio di base degli accoppiatori oleodinamici. Si tratta di componenti costituiti principalmente da due giranti (pompa e turbina) racchiuse in un involucro sigillato che contiene un fluido (in genere olio).
- Girante pompa: Connessa all’albero motore, spinge il fluido verso la girante turbina.
- Girante turbina: Riceve l’energia dal fluido in movimento e la trasmette all’albero di uscita, trasferendo così la coppia.
Questo meccanismo assicura un avvio graduale e limita le vibrazioni, poiché la trasmissione della potenza non avviene per contatto diretto tra parti meccaniche, ma sfrutta l’azione dinamica del fluido.
Negli ultimi anni, le aziende del settore hanno lavorato su design che ottimizzano i flussi interni, riducono le turbolenze e migliorano la dissipazione del calore, aumentando così l’efficienza e la durata operativa.
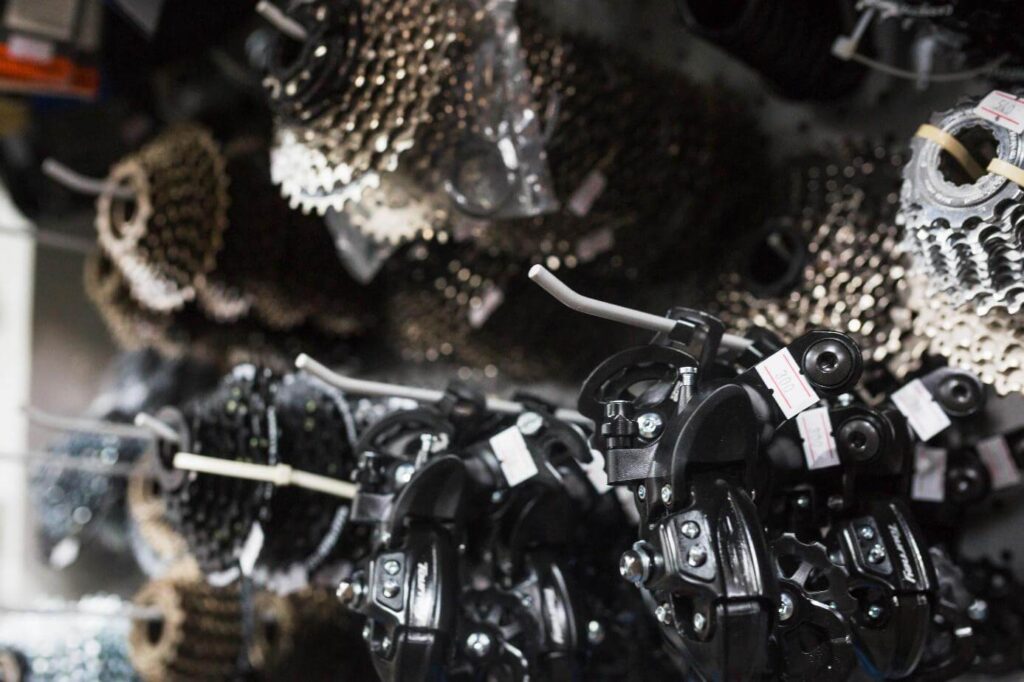
Materiali avanzati e resistenze termiche migliorate
Uno degli aspetti più interessanti delle recenti innovazioni negli accoppiatori oleodinamici riguarda la scelta dei materiali. Se tradizionalmente si utilizzavano leghe metalliche standard (come acciai al carbonio o ghise speciali), ora si stanno diffondendo soluzioni con acciai legati ad alta resistenza, leghe di alluminio e perfino compositi.
- Migliore conducibilità termica: L’impiego di materiali con conducibilità termica superiore consente di dissipare il calore generato dagli attriti e dalle turbolenze in modo più rapido, garantendo una temperatura di esercizio più stabile.
- Peso ridotto: L’uso di leghe leggere, in particolare quelle a base di alluminio, riduce la massa complessiva del componente. In applicazioni come i veicoli industriali o macchine operatrici, un minor peso si traduce in un miglior rapporto prestazioni/consumi.
- Aumento della durabilità: Trattamenti superficiali avanzati, come rivestimenti ceramici o termici, riducono l’usura e prolungano la vita utile dell’accoppiatore, con conseguenti risparmi sui costi di manutenzione.
Queste scelte di materiali e trattamenti hanno permesso agli accoppiatori oleodinamici di raggiungere livelli di affidabilità molto più elevati, anche in condizioni operative estreme (ambienti ad alte temperature, carichi elevati, atmosfere corrosive).
Sensori integrati e manutenzione predittiva
Un’altra rilevante tendenza innovativa è l’integrazione di sensori all’interno degli accoppiatori oleodinamici. Grazie all’Industrial Internet of Things (IIoT), oggi è possibile dotare i macchinari di sensori che misurano parametri fondamentali come:
- Temperatura del fluido: Un controllo costante del calore garantisce un funzionamento stabile e previene surriscaldamenti anomali.
- Livello di vibrazioni: Vibrazioni eccessive possono indicare malfunzionamenti o usura interna.
- Pressione e portata del fluido: Variazioni improvvise di pressione o portata possono segnalare problemi di tenuta o usura delle giranti.
Questi dati, raccolti in tempo reale, vengono inviati a sistemi di supervisione e analisi che consentono di attivare la manutenzione predittiva. In questo modo, i tecnici possono intervenire prima che si verifichino guasti catastrofici, ottimizzando la pianificazione dei fermi macchina e riducendo al minimo i costi di fermo impianto.
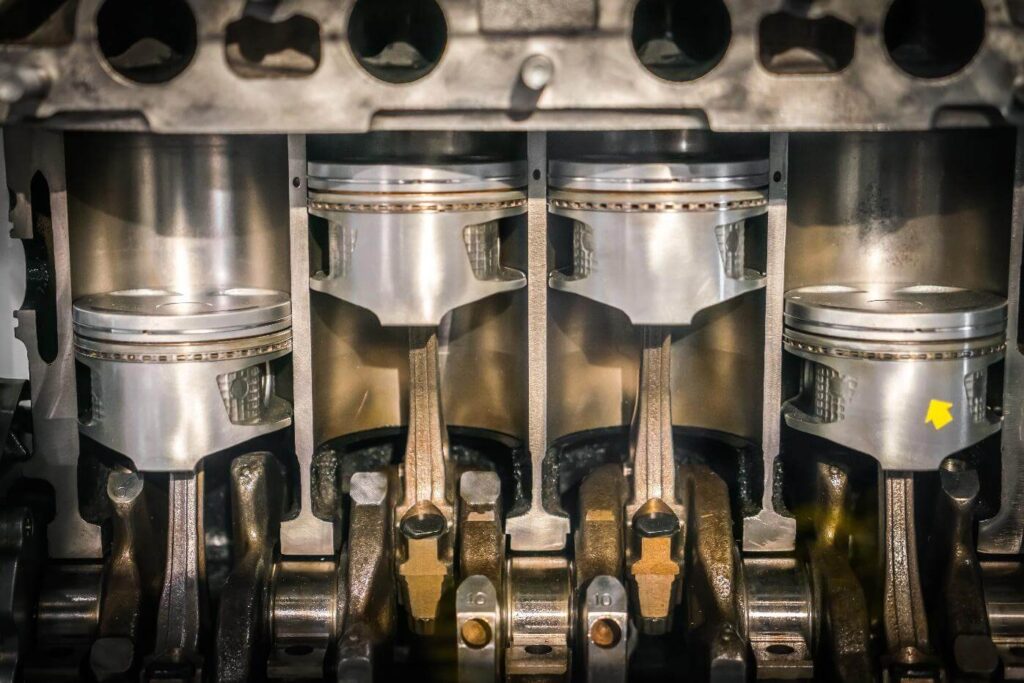
Ottimizzazione fluidodinamica per una maggiore efficienza
Oltre all’aspetto dei materiali e dei sensori, i produttori di accoppiatori oleodinamici stanno concentrando i propri sforzi sul design interno delle giranti e sui percorsi del fluido. L’uso di software di simulazione CFD (Computational Fluid Dynamics) ha aperto la strada a:
- Giranti con geometrie innovative: Profili ottimizzati che riducono al minimo la turbolenza, aumentando la quantità di energia effettivamente trasmessa.
- Riduzione delle perdite: Canali di circolazione del fluido studiati per evitare ristagni e aumentare la portata utile.
- Controllo della cavitazione: La cavitazione, fenomeno dovuto a rapidi cambi di pressione che generano micro-bolle nel fluido, può erodere le superfici interne. Design avanzati aiutano a minimizzare tale effetto e a preservare l’integrità dell’accoppiatore.
Tutto ciò si traduce in un miglior rendimento, inteso come maggiore frazione di energia meccanica trasmessa dal motore al carico. Con rendimenti più elevati, si possono ridurre i consumi e migliorare la sostenibilità energetica dell’intero impianto.
Evoluzione dei sistemi di controllo e digitalizzazione
Negli impianti di ultima generazione, gli accoppiatori oleodinamici non sono più elementi isolati, ma si integrano in un ecosistema di controllo e monitoraggio. Questo avviene mediante:
- PLC e sistemi SCADA: I dati provenienti dai sensori dell’accoppiatore vengono inviati a unità di controllo che regolano parametri come velocità, coppia e flusso di fluido, in base alle esigenze operative.
- Controllo proporzionale: Tecnologie di valvole proporzionali o servovalvole possono regolare in tempo reale la quantità di fluido nell’accoppiatore, ottimizzando la trasmissione di potenza e riducendo sprechi energetici.
- Integrazione con reti industriali: Ethernet industriale, bus di campo (es. Profibus, CANopen) e protocolli di comunicazione remota consentono di collegare gli accoppiatori a piattaforme centralizzate di gestione degli impianti, facilitando interventi di manutenzione da remoto e analisi big data.
Questo approccio “smart” non solo massimizza l’efficienza, ma contribuisce a ridurre i fermi imprevisti e ad allungare la vita utile dei componenti.
Integrazione con i sistemi di recupero energetico
Un trend sempre più in voga è l’integrazione degli accoppiatori oleodinamici con sistemi di recupero energetico, specialmente nei processi industriali a ciclo continuo. L’energia dissipata sotto forma di calore o perdita idrodinamica può essere parzialmente recuperata attraverso:
- Scambiatori di calore ad alta efficienza: In grado di captare l’energia termica dispersa e riutilizzarla in altri processi (ad esempio riscaldamento di fluidi di processo o pre-riscaldamento di acqua).
- Generatori ausiliari: Sistemi che sfruttano la portata del fluido in movimento per alimentare piccoli generatori elettrici, riducendo il consumo di corrente dalla rete principale.
Queste soluzioni, seppur ancora in fase di sviluppo, promettono di ridurre notevolmente l’impatto energetico dell’intero impianto e di rendere più sostenibili i processi industriali in cui gli accoppiatori oleodinamici vengono impiegati.
Conclusioni e prospettive future
L’universo degli accoppiatori oleodinamici è in costante evoluzione. Le innovazioni riguardano principalmente quattro aree: materiali, design fluidodinamico, sensoristica integrata e sistemi di controllo digitali. Questa combinazione di avanzamenti tecnologici ha permesso di migliorare in modo significativo l’efficienza, l’affidabilità e la sostenibilità delle trasmissioni idrodinamiche.
Guardando al futuro, possiamo prevedere uno scenario in cui gli accoppiatori oleodinamici diventeranno sempre più intelligenti e interconnessi, grazie all’ulteriore sviluppo dell’Internet of Things industriale. La tendenza verso la manutenzione predittiva si rafforzerà, supportata da modelli di intelligenza artificiale in grado di analizzare grandi quantità di dati operativi in tempo reale e fornire interventi di regolazione immediati.
Inoltre, la spinta verso l’efficienza energetica e la riduzione delle emissioni continuerà a stimolare la ricerca su materiali leggeri, rivestimenti a bassissimo attrito e soluzioni di recupero energetico ancora più efficaci. In settori come quello automotive, navale e dell’energia rinnovabile, le applicazioni di accoppiatori oleodinamici di nuova generazione porteranno a un abbattimento dei costi di esercizio e a un minore impatto ambientale.
In conclusione, gli accoppiatori oleodinamici rappresentano un componente chiave per la trasmissione di potenza in molteplici ambiti industriali. Le recenti innovazioni non solo rispondono alle sfide del presente, ma pongono solide basi per un futuro sempre più orientato alla digitalizzazione, alla sostenibilità e all’efficienza. Chi investe oggi in soluzioni d’avanguardia potrà trarre beneficio da sistemi di produzione più competitivi, affidabili e rispettosi dell’ambiente.