Nel settore manifatturiero e produttivo, le macchine industriali sono il cuore di ogni attività. Senza di esse, i processi di lavorazione, assemblaggio e confezionamento subirebbero rallentamenti o addirittura arresti improvvisi, con gravi conseguenze a livello economico e logistico.
La riparazione di macchine industriali diventa quindi un tema cruciale per garantire efficienza, produttività e competitività sul mercato. In questo articolo, approfondiremo quando e perché la riparazione diventa necessaria, come pianificarla e quali strategie adottare per prevenire e ridurre i costi legati ai fermi macchina.
L’Importanza di Mantenere le Macchine Industriali in Perfetto Stato
In ogni impianto produttivo, il buono stato delle macchine industriali è direttamente correlato alla redditività dell’azienda. Quando i macchinari lavorano correttamente:
- Aumenta la produttività: tempi morti ridotti, cicli di produzione più rapidi e consegne puntuali.
- Si riducono i costi di gestione: meno sprechi, meno scarti di produzione e un minor consumo energetico.
- Cresce la soddisfazione del cliente: consegne puntuali e prodotti con standard di qualità elevati.
- Si migliora la sicurezza sul luogo di lavoro: macchine ben manutenute riducono i rischi di infortuni.
Tuttavia, per quanto si possa prevenire, il guasto è sempre dietro l’angolo. Fattori come l’usura dei componenti, l’uso intensivo e talvolta la scarsa manutenzione possono portare a guasti, anche gravi, che richiedono riparazioni immediate.
Quando è Necessaria la Riparazione: Fattori di Rischio e Segnali di Allarme
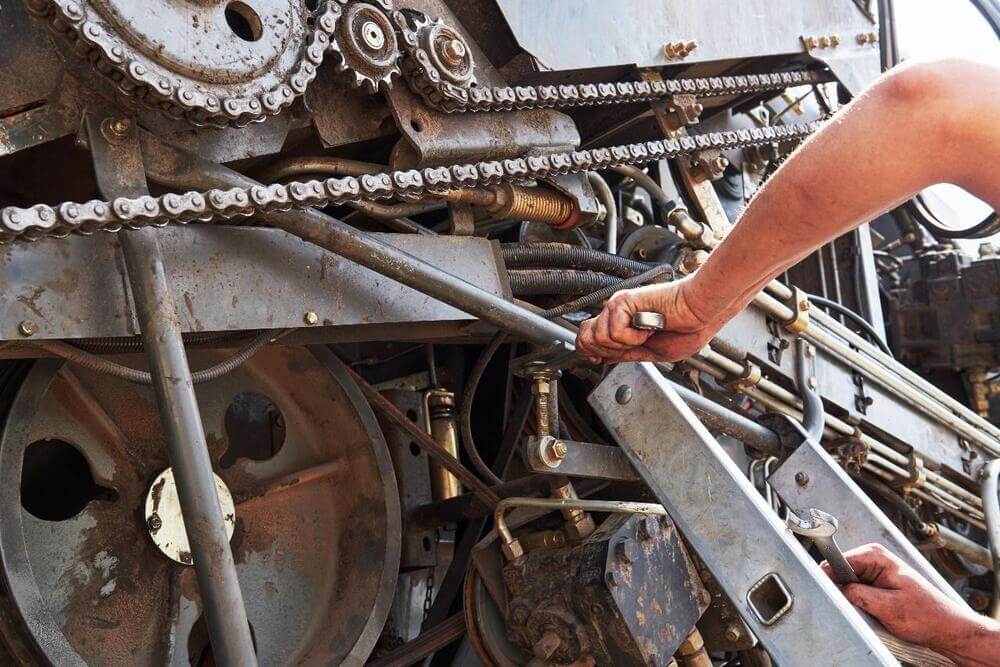
Non tutte le anomalie che si presentano in una macchina industriale implicano un guasto irreparabile; spesso, si tratta di piccoli malfunzionamenti che possono essere risolti con una manutenzione ordinaria. Tuttavia, esistono situazioni in cui la riparazione diventa un passaggio obbligato:
Diminuzione delle Prestazioni
Se il rendimento di una macchina cala in modo significativo, ad esempio se impiega più tempo a eseguire lo stesso ciclo produttivo o se genera scarti in misura superiore alla norma, potrebbe essere indice di un componente che si sta danneggiando. In questi casi, una riparazione tempestiva può evitare che il problema si aggravi, provocando un fermo macchina costoso.
Rumori e Vibrazioni Anomale
Un altro segnale di allarme è la comparsa di rumori insoliti o vibrazioni anomale durante il funzionamento. Questi fenomeni possono dipendere da cuscinetti usurati, parti mal allineate o componenti non ben lubrificati. Se non si interviene rapidamente, il rischio di danni meccanici gravi aumenta in modo esponenziale.
Temperature Elevate e Surriscaldamenti
Surriscaldamenti anomali o picchi di temperatura sono spesso spie di un malfunzionamento del sistema di raffreddamento o di un sovraccarico di lavoro. Proseguire la produzione in queste condizioni può portare a deformazioni dei materiali, rotture e rischi per la sicurezza del personale.
Fermi Macchina Ripetuti
Se l’impianto si blocca più volte nell’arco di breve tempo, è segnale che la manutenzione preventiva non è sufficiente o che vi sia un problema strutturale. In questi casi, è fondamentale procedere con un’analisi approfondita e una riparazione integrale per individuare e risolvere la causa alla radice, evitando ulteriori perdite di produzione.
Perché la Riparazione è Fondamentale: Vantaggi e Benefici
La riparazione di macchine industriali non è solo un “male necessario”, ma rappresenta un’occasione per migliorare l’efficienza dell’impianto e ottimizzare i processi produttivi. Ecco alcuni vantaggi tangibili:
- Allungamento della Vita Utile dei Macchinari
Intervenire per tempo su componenti danneggiati permette di prolungare la vita utile dell’impianto, posticipando l’investimento in nuove attrezzature. - Riduzione dei Costi di Fermo Macchina
Un guasto improvviso genera costi elevati legati a ritardi nelle consegne e penali contrattuali. Programmare riparazioni mirate consente di minimizzare i tempi di inattività. - Sicurezza e Conformità Normativa
Assicurare che le macchine siano sempre in condizioni ottimali riduce il rischio di incidenti sul lavoro e garantisce il rispetto delle normative vigenti in materia di sicurezza. - Miglioramento della Qualità Produttiva
Macchinari ben manutenuti e riparati correttamente conservano la precisione e la costanza necessarie per garantire standard di qualità elevati.
Manutenzione Ordinaria vs. Manutenzione Straordinaria
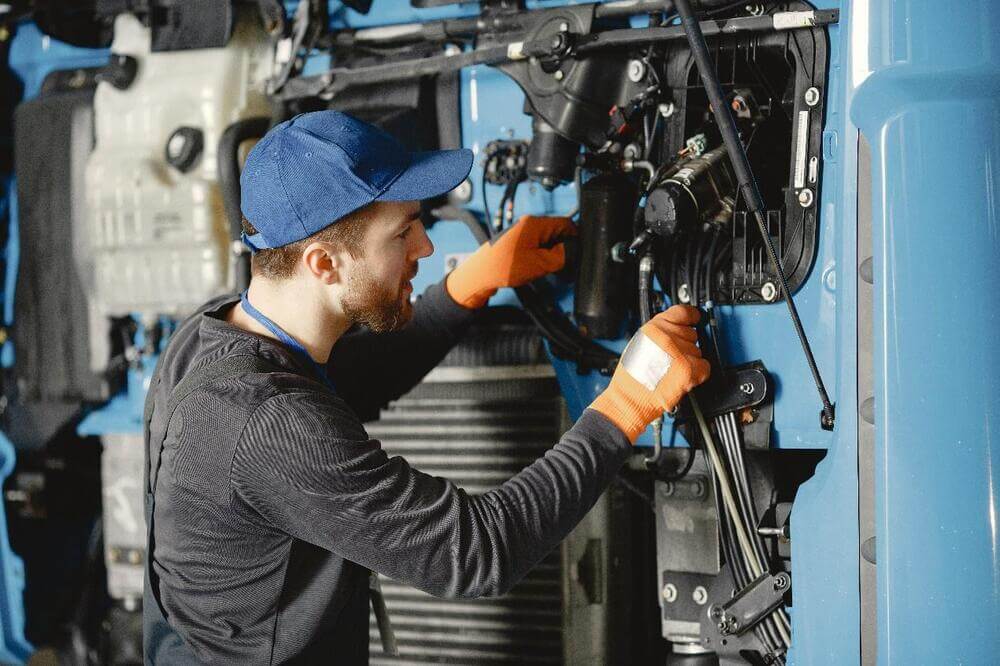
Spesso, quando si parla di riparazione di macchine industriali, si fa riferimento alla manutenzione straordinaria: l’intervento necessario per ripristinare la funzionalità dopo un guasto. Tuttavia, una manutenzione ordinaria efficace può prevenire gran parte dei problemi e ridurre al minimo la necessità di riparazioni costose.
- Manutenzione Ordinaria: include controlli periodici, sostituzione programmata di componenti soggetti a usura (come filtri, cinghie e cuscinetti), lubrificazione e pulizia. Queste operazioni consentono di identificare i segnali di allarme in fase iniziale.
- Manutenzione Straordinaria: si esegue in seguito a un guasto grave o a una rottura imprevista. In questo caso, i costi sono generalmente più elevati, perché l’intervento richiede materiali specifici, personale esperto e, spesso, il fermo dell’impianto per un periodo significativo.
Come Pianificare un Programma di Riparazione Efficace
Un approccio vincente alla riparazione di macchine industriali si basa su una pianificazione strategica che tenga conto delle esigenze produttive e delle caratteristiche specifiche dei macchinari. Alcune linee guida da seguire:
- Analisi dei Dati Storici
Raccogliere e analizzare i dati sulle precedenti manutenzioni, i tipi di guasto più frequenti e le parti più soggette a usura. Questo aiuta a prevedere i possibili malfunzionamenti e a programmare interventi mirati. - Priorità sugli Impianti Critici
In ogni stabilimento esistono macchine più critiche di altre, per via dell’importanza nel processo o del costo di fermo. Identificare questi impianti e prevedere controlli aggiuntivi può ridurre i rischi di fermo improvviso. - Formazione del Personale
Spesso, la prima linea di difesa è rappresentata dagli operatori. Se il personale è formato per riconoscere tempestivamente suoni insoliti, vibrazioni anomale o cali di prestazione, si possono ridurre i tempi di reazione e i danni complessivi. - Implementazione di Sistemi di Monitoraggio Predittivo
Le moderne tecnologie, come i sensori IoT e i software di analisi dei dati, consentono di tenere sotto controllo lo stato di salute dei macchinari in tempo reale, prevenendo guasti e individuando le anomalie prima che si trasformino in problemi gravi.
Scegliere il Partner Giusto per la Riparazione
Nella maggior parte dei casi, le aziende si affidano a fornitori di servizi specializzati o ai centri di assistenza ufficiali dei costruttori di macchinari. La scelta del partner giusto è determinante per garantire interventi tempestivi e risolutivi. Ecco alcuni criteri di selezione:
- Esperienza e Competenza: verifica che il fornitore abbia personale qualificato, conoscenza approfondita dei macchinari e una solida reputazione sul mercato.
- Disponibilità di Ricambi Originali: per preservare la qualità del macchinario, è preferibile utilizzare componenti e ricambi originali o certificati.
- Tempestività: in caso di guasto, ogni ora di fermo macchina ha un costo. Un servizio di assistenza rapido e disponibile 24/7 può fare la differenza.
- Servizi Aggiuntivi: alcune aziende offrono pacchetti integrati di manutenzione preventiva e interventi straordinari, con contratti di servizio che garantiscono costi predeterminati e priorità di intervento.
Costi e Ritorno sull’Investimento
Un aspetto che spesso preoccupa i responsabili aziendali riguarda i costi di riparazione. Tuttavia, è fondamentale considerare il ritorno sull’investimento (ROI): intervenire tempestivamente su una macchina guasta può evitare fermi produttivi molto più costosi. Alcuni punti da valutare:
- Costo Diretto della Riparazione: materiali, manodopera e possibile sostituzione di componenti.
- Perdita di Produzione: calo degli output, possibili penali per ritardi nelle consegne.
- Costi di Sicurezza: un guasto non risolto può causare incidenti sul lavoro, con conseguenze legali ed economiche di notevole entità.
- Obsolescenza Tecnologica: in alcuni casi, la riparazione può includere l’aggiornamento del macchinario, migliorando l’efficienza e allineandolo agli standard più recenti.
Spesso, il costo iniziale di una riparazione adeguata si ripaga in breve tempo, grazie all’aumento della produttività e alla riduzione delle spese legate a guasti ricorrenti.
Conclusioni: Investire Oggi per Risparmiare Domani
La riparazione di macchine industriali non è solo una spesa inevitabile, ma un vero e proprio investimento nella competitività dell’azienda. Affrontare tempestivamente i malfunzionamenti, implementare un programma di manutenzione strutturato e formare il personale consente di allungare la vita dei macchinari, ridurre i fermi produttivi e mantenere alti gli standard qualitativi. Nel contesto industriale moderno, caratterizzato da mercati globali e ritmi produttivi serrati, non si può prescindere da un approccio proattivo e lungimirante.
Investire in riparazioni di qualità e in una manutenzione preventiva ben pianificata significa assicurarsi una maggiore efficienza operativa, rispettare gli obblighi normativi in materia di sicurezza e, soprattutto, rimanere competitivi. Ogni azienda che intenda ottimizzare i propri processi e difendere la propria quota di mercato dovrebbe valutare con attenzione le strategie di assistenza tecnica e riparazione, puntando su partner affidabili e su soluzioni tecnologiche all’avanguardia.
Se gestire le risorse con attenzione fa parte della filosofia aziendale, allora la riparazione delle macchine industriali diventa un tassello fondamentale del mosaico operativo, perché garantisce continuità produttiva, riduce i rischi e tutela la redditività complessiva dell’intero processo.